Molybdenum is not a name that rolls off the tongue easily. Nor does it spark instant public recognition like other minerals such as gold, platinum or even iron ore. It’s a rare earth metal, prized as an alloy in electronics for its conductivity, softness and thermal properties. Still, molybdenum’s claim to uniqueness extends further than its arcane high-performance industrial uses – a source of molybdenum is the first mineral deposit to be discovered solely through AI.
At the end of October, Earth AI, an Australian explorer for clean energy metals, announced it had found a molybdenum deposit in New South Wales. Earth AI claimed it was the world’s first ever AI-discovered greenfield deposit.
‘High molybdenum grades were confirmed in three samples analysed by a certified laboratory. These grades, registered at 0.3%, 0.26% and 0.135%, exceed the currently mined grades of 0.16% and 0.14% found in the world’s two leading molybdenum mines,’ according to a report in BusinessWire.
‘Earth AI’s porphyry molybdenum deposit discovery showcases how the company is addressing the shortage of critical metals by making mineral exploration precise and scalable for the first time. Discovery rates for these metals are at their lowest levels ever, with costs at their highest, causing a major supply gap that will continue to widen. Traditional metals exploration is costly, unreliable and environmentally harmful, with an average 1 in 200 success rate and US$100 million per discovery. Earth AI’s porphyry molybdenum deposit discovery had a one in eight success rate and a cost of US$2 million, attributed to advanced AI prediction tools that are set to revolutionise the economics of mining for energy transition metals,’ according to the report.
It quotes the company’s CEO Roman Teslyuk as saying that it ‘showcases a significant stride toward challenging the industry’s traditional norms, and we are unveiling a pathway to mineral discovery that is not only faster and more economical but also exceptionally precise’.
Mining has always been at the forefront of developing new tech, a trend that has grown in recent years especially in the light of the adoption of data analysing of every aspect of a mine’s operations in an effort to cut costs, increase worker safety and enhance productivity and efficiency. Now the latest technological development – AI – is set to disruptive the industry even more.
‘In exploration, mining technology for value is about taking geoscience information and figuring out where the quality of the bodies [of minerals] are, and how best to get that ore body and take it out,’ Nishal Nair, MD of resources at Accenture, told Mining Review Africa. He added that AI stands out as a game-changing mining technology, setting the stage for unprecedented efficiency and sustainability.
‘Another application of AI in the mining industry is exploration. It’s time-consuming, costly, and involves sifting through tons of data to prospect more accurately.’
That aspect of the tech is something that Earth AI’s molybdenum deposit discovery has highlighted perfectly.
Nair says AI offers much more to the industry than serious data crunching as it can shape monitoring, ‘predictive maintenance, and even health and safety applications’.
AI stands to be a good enabler for the mining sector with the adoption of unmanned equipment and machinery, according to an opinion article by Heinrich Jantzen, senior mining adviser at consulting engineering and infrastructure advisory company Zutari.
He says the industry is already well acquainted with extracting smart data from sensors. However, he adds, while sensors are critical to generating data and early warning of any risks, it is AI that will ensure robust, reliable and actionable data.
‘Mines face a complex range of operational challenges that make everything quite risk averse. That is really when it boils down to technology driving the status quo. It is about the combination of all these factors and increasing the focus on collaborative adoption of technological solutions.
‘It is a matter of how mining will take advantage of such developments in both the broader industry and individual mining operations themselves. The question is how you apply such advances within the mining space, as the industry strives to become a safer occupation and a more sustainable industry. I think the future is quite rosy in terms of AI.’
Jantzen says the ‘current focus of unlocking value in mining by means of technology looks at how workers interface with machines themselves. Digital transformation continues to drive this process across the entire industry. Mining is pushing the envelope in terms of the remote operation of heavy equipment’.
‘The questions that need to be answered are how much can be done remotely, what is the capability to monitor such remote operations, and how to achieve the automation of fixed heavy assets. This is the ideal combination for mining in terms of what technology can achieve,’ he says.
An example of this new way of thinking about existing assets is illustrated by South African company Sibanye-Stillwater, which has substantial mining assets both on the continent and in the US. Sibanye-Stillwater used Mosimtec, an American provider of computer simulation consulting services, to construct a virtual digital twin of its Stillwater platinum/palladium mine near the town of Nye in Montana.
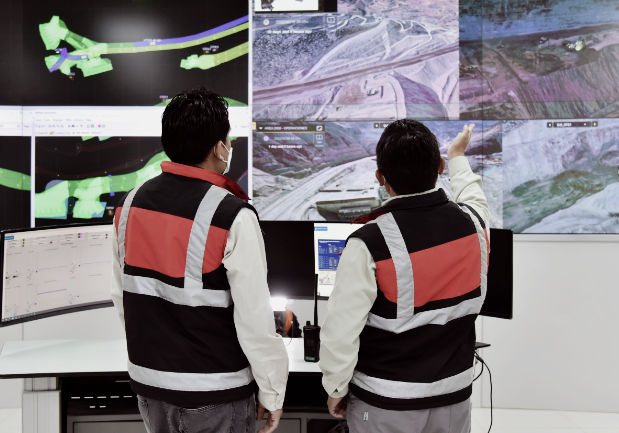
According to an opinion article in Mining Review Africa by consultants from Deloitte, the aim of the digital twin mine was ‘to create a single intelligent system to predict overall system capacity and schedule delivery of backfill to better match the mine plan. The digital twin integrates with corporate IT systems for data inputs and outputs and can provide the ability to automatically or manually run scenarios to compare risks and surpluses and proactively adjust plans to mitigate bottlenecks. Sibanye-Stillwater estimates that, following implementation of the model, backfill modelling and scheduling now take 20 minutes instead of two to three hours per week, and bottlenecks and sequencing issues can be identified and proactively addressed months in advance’.
Sibanye-Stillwater was an early and enthusiastic adopter of AI-driven tech. In 2019, the company announced it had hired Cape Town-based firm DataProphet, an AI and machine learning specialist, to use AI to extract value from historical data and optimise manufacturing and mineral processing plants.
‘Artificial intelligence in processing facilities has presented itself as an extremely exciting prospect for us through previous research, development and implementation of similar, less technologically advanced initiatives in the past,’ according to a statement by Sibanye-Stillwater’s technology and innovation lead Alex Fenn. ‘As the initiative deals with the back-end of our value chain, the primary returns are almost wholly reflected in our bottom line and, at the scale at which we operate, are generally several orders of magnitude larger than the investment required to achieve them.’
Meanwhile, taking AI to even greater heights is Angolan state-owned diamond company Endiama. It has partnered with the country’s National Space Programme Management Office to launch Tech-Minas, a tool that combines AI use with satellite imagery to map and monitor ‘diamond-related activities’ in Angola.
Endiama says it will help prevent illegal diamond mining and allow more efficient tracking of the gem’s entire value chain.
Perhaps the ultimate example of embracing the value of technology is Rio Tinto’s Gudai-Darri iron ore mine in Australia. It ‘features an unprecedented deployment of technology, much of it industry-leading’, according to the miner. The suite of innovation includes autonomous trucks and drills (‘the trucks implement real-time ore tracking using sensors to provide live dig face progression, while data-informed modelling from the drills helps to build more accurate assessments of existing ground conditions and improve safety’); autonomous water carts (‘the vehicle’s intelligent on-board system detects dry and dusty conditions on-site, triggering the application of water to roads to keep them in good condition’); a robotic ore sampling laboratory (‘production samples enter the lab via a conveyor from the sample station and will be transferred to the automated production cell by a robot’); robotics in the heavy mobile equipment warehouse (‘home to four automatic guided vehicles designed to automate the handling of pallet frames’); paperless field mobility (‘through tablets, team members can access many of the applications they require out in the field thereby eliminating the need for paper-based systems and reducing unnecessary travel’); a digital twin asset (‘will enable our team members to visually navigate the asset and plan their work using a 3D model’) and all of this will be powered by a solar farm (‘consists of about 83 000 solar panels with a capacity up to 34 MW’).
The future of mining is clear – it will increasingly be entwined with a technology-driven landscape.