It takes more than an hour to get from the surface to the deepest parts of Harmony Gold’s Mponeng gold mine. There, 4 km below ground, the temperature of the rock face is a blistering 65°C and the air is a thick 30°C – and that’s only after it has been cooled by slurry ice pumped in to make the environment tolerable for humans.
Mponeng is the world’s deepest mine, topping a list that’s dominated by South African operations. Those unique conditions require highly specialised mining equipment, and a deep understanding of the local environment. Yet historically, precious little of the equipment used in South Africa’s – or Africa’s – mines has been developed or produced locally.
As Arne Frandsen, managing partner at the Pallinghurst Group, told Mining Weekly, ‘for hundreds of years, people have come to Africa to take the resources and basically add the value to them back home, somewhere else. Value-adding was kept to a minimum’.
Pallinghurst is a shareholder in platinum group metals (PGMs) producer Sedibelo Platinum Mines, which recently announced the construction of a Kell processing plant at Pilanesberg Platinum Mines, in South Africa’s North West province. The plant uses just 18% of the electricity used by conventional PGM smelting and – here’s the kicker – it refines its PGMs on-site. As Frandsen explains, ‘we can actually take everything up out of the ground in Pilanesberg, and we can deliver the final product to the end consumer’.
Sedibelo’s on-site processing plant is part of a growing move towards African mining equipment, made in Africa, by Africans, for African mining conditions. Lubumbashi-based Congo Equipment, for example, has a localisation training plan that aims to replace the company’s expatriate workforce with Congolese nationals. CEO Noel Mabuma, in a Global Business Reports interview, says critical positions have been identified and matched with nationals who are being trained to take over the position. ‘Even if the law was not strictly enforced with regard to the transfer of skill, we believe this is how we give back to the country and community in which we operate.’
In February 2020, Congo Equipment opened a US$40 million facility consisting of workshops, warehouses and offices, as well as a new component rebuild centre, where local technicians can rebuild transmissions, engines and so on.
‘Local content is not enforced greatly in the DRC,’ says Mabuma. ‘However, I believe this will change, as the government wishes to implement it in the upcoming months.’
South Africa is there already. As stipulated by the country’s Mining Charter III, a minimum of 70% (by value) of mining goods used in South Africa must be manufactured or assembled in South Africa, and at least 60% local content must be used during manufacture or assembly.
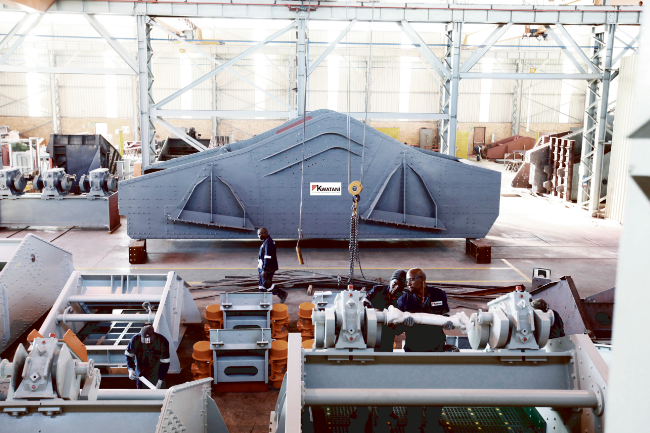
Local industry body Mining Equipment Manufacturers of South Africa requires its members to commit to 60% local sourcing. CEO Lehlohonolo Molloyi sees local innovation as key to achieving this.
‘It is quite clear that the [intellectual property] issue of foreign OEMs needs to be addressed,’ he says. ‘Too many foreign entities hold onto key technologies and, at some point, we need to find ways to bring innovation back into the hands of local South African manufacturers. This innovation then needs to be shared with the rest of the continent. Foreign OEMs hold a sizeable share of the market, but if these companies are serious about the future of mining on the African continent, they should share their intellectual property and allow the rest of the continent to have access to it.’
Molloyi hails the Sibanye-Stillwater and Wits University’s DigiMine initiative as being ‘a clear example that South African higher-learning institutions, together with mining manufacturers, have what it takes to be global leaders in innovation and mining IP’.
Over and above the promise of improved safety and sustainability, in-country mining-equipment producers also offer the benefits of being quick, customised and (especially important during the ongoing global supply-chain crisis) close by.
Steinmüller Africa, for example, boasts a Cojafex PB 850 induction bending machine (one of just two in Africa) that enables petrochemical and mining plants to source custom induction bends locally – and quickly.
Induction bending is the process whereby a straight pipe is precision-bent by a specially engineered machine, explains Lee Chapman, divisional manager of piping at Steinmüller Africa. ‘It’s ideal when standard-size bends are not available and custom or large radius bends are required.’
Chapman adds that Steinmüller Africa also offers complementary services, ‘so there is no need to move the component between different suppliers as we are able to do all the necessary bending, welding and heat treatment in-house’.
South African OEM Kwatani, meanwhile, delivers custom-designed vibrating equipment within time frames similar to those offered by OEMs that deliver standard equipment. ‘Our processes are based on a job-based system, so the entire production-facility layout is arranged in a job-process environment, where all processes are highly streamlined,’ says Kwatani CEO Kim Schoepflin. And while that fast turnaround time is largely due to the production processes at its 17 000 m² facility in Kempton Park, Gauteng, it’s a local company producing bespoke equipment, right in the heart of South Africa’s mining country.
Vibramech is in a similar position. The company has clients in Mali, Liberia, Sierra Leone, Mauritania, Guinea, Senegal, Ghana, Burkina Faso and Côte d’Ivoire, and its equipment is manufactured in-house at its factory in Chamdor, just up the road from Harmony’s Doornkop gold mine in Gauteng. Vibramech’s vibrating equipment is custom-designed for Africa’s harsh, above-ground operating conditions, which – as MD David Massey points out – are highly diversified from one country to the next.
By using local OEMs, Africa’s mining houses can bypass the long (and increasingly unreliable) global supply chain. That much was clear at the 2021 annual conference of the Rapid Product Development Association of South Africa (RAPDASA), which represents the local additive manufacturing (AM) industry.
AM, which is more popularly known as 3D printing, has provided a much-needed solution to the critical needs created by the COVID-19 crisis – as RAPDASA chair Marius Vermeulen underlines.
‘At the human level COVID has been terrible. But it placed a lot of focus on AM technology, globally, from the media. This was for two reasons,’ he says.
‘First, the rapid nature of the technology, which resulted in many product developments during the pandemic, aimed at combating it, which were only possible because of the speed AM provides. Second, the beneficial impact the technology can have on logistics chains: AM allowed the local manufacture of certain products – for example, face shields.’
And, he emphasises, ‘in South Africa, supply-chain problems resulting from the impact of COVID have stimulated consideration of what input components, previously imported, could be produced locally through AM’.
Mining giant Anglo American confirmed the value of AM when, in May 2021, it partnered with the South African Council for Scientific and Industrial Research and US-based tech company Ivaldi Group to explore opportunities to digitally distribute spare parts for mining and processing equipment – manufactured locally using 3D printing.
‘The ability to send files – not physical spare parts – will reduce our carbon footprint, delivery lead times and logistics costs,’ according to Matthew Chadwick, head of socio-economic development and partnerships at Anglo American. ‘Importantly, this has the clear potential to create industrial and service jobs for host communities and surrounding regions through on-demand manufacturing systems to produce spare parts locally.’
The project ticks all the boxes in the argument in favour of locally produced equipment. Once its spare-parts inventory is fully digitalised, Anglo American will be able to meet the Mining Charter III requirements while producing parts and equipment quickly and locally – and to the exact unique requirements of the company’s many deep (and dangerous) mines.