Mining is a cornerstone of Africa’s economy, providing essential resources for industries worldwide. Of course, it goes without saying that mining is inherently dangerous and demanding. With massive machinery in constant motion and challenging underground environments, safety remains of paramount concern.
South Africa’s mining industry recorded a total of 55 fatalities during 2023, a 12% increase from the previous year.
‘Before the single incident in November in which 13 employees died, we were tracking well compared to 2022 and we were trending well on our path to zero harm. It was a real shock for the industry,’ says Japie Fullard, chair of the CEO Zero Harm Forum. In late November last year, 86 employees were involved in a winder accident at Impala Rustenburg’s 11 Shaft operation, 13 of whom lost their lives.
‘Safety is not a competition and we are all in this together,’ according to Fullard. ‘We share safety learnings among ourselves as CEOs and executives, and we take this process very seriously.’
Realising the full potential of technology in enhancing safety requires collaboration among mining companies, technology providers, regulators and other stakeholders.
The CEO Zero Harm Forum is a collaboration between the Minerals Council South Africa (MCSA) and the CEOs of more than 30 mining companies. Founded in 2012, the forum was established to drive health and safety initiatives in the sector, while addressing key challenges in a bid to accelerate the journey to zero harm – premised on the notion that the industry’s CEOs need to lead by example.
One of the forum’s key focus areas is falls of ground, which remain the largest cause of fatalities in the industry.
Five years after its inception, the CEO Zero Harm Forum established Khumbul’ekhaya (from the Nguni term for ‘remember home’), to further catalyse and uphold the industry’s pursuit of zero harm.
Sietse van der Woude, senior executive of modernisation and safety at the MCSA, adds that ‘mining cannot modernise without innovation, and often this innovation stems from outside the mining ecosystem’.
Case in point is the work under way at the Mandela Mining Precinct, a public-private partnership between the South African Department of Science and Innovation and the MCSA. One of the many projects it is working on is a mechanised drill and blast programme, which according to the precinct, ‘is targeted at providing sustainable, mechanised solutions to the gold and platinum mining industries by introducing disruptive technologies to facilitate zero harm and achieve financially sound underground mining operations with consistent production rates at optimal cost’.
In recent years, there has been a rapidly growing emphasis on leveraging technology – with a focus of automation and mechanisation – to enhance safety standards in African mines. Mining automation has flourished into a multibillion-dollar industry, with operators globally dedicating substantial investments to advance and implement autonomous fleets. Projections indicate a significant threefold increase in smart-mining operations by 2025.
Advancements in areas such as automation, mechanisation, remote monitoring and data analytics have the potential to transform safety practices by delegating the tasks once performed by human miners – particularly in dangerous conditions, such as drilling – to technology. For instance, autonomous vehicles can navigate hazardous terrain without putting human operators at risk. Similarly, drones equipped with sensors can conduct aerial inspections, identifying potential safety hazards more efficiently than traditional methods.
In 2016, Rio Tinto – one of the world’s largest mining companies – was the first in the world to transport all of its iron ore via driverless trucks and vehicles. Through its Mine of the Future initiative, it has deployed autonomous haul trucks, drilling rigs and trains across its operations, significantly reducing safety incidents and improving operational efficiency.
Anglo American’s FutureSmart Mining programme, meanwhile, integrates innovative technologies, such as remote-controlled drones, underground WiFi networks and advanced analytics platforms to enhance safety and sustainability in its operations.
Anglo American subsidiary Amplats is using mechanisation in its mining operations to ensure the safety of their employees, improve efficiency and reduce costs. Its transition towards mechanisation, partly motivated by investor concerns regarding ethical returns, has yielded substantial safety benefits. As of April 2024, there had been ‘no fatalities at our operations in the past 27 months, which is our longest fatality-free period. We are continuing with the focused implementation of our safety practices to ensure that each of our colleagues returns home safely every day’, the company notes in a media statement.
Like many of its contemporaries, Amplats places consistent emphasis on prioritising safety measures.
‘We are maximising value […] through operational and marketing excellence, modernisation and technology to remain resilient through commodity price cycles. We are resetting benchmark performance with modernisation and mechanisation work at Amandelbult,’ according to CEO Craig Miller. ‘Safety at Amandelbult has improved significantly, with the operation achieving three consecutive years fatality-free and 10 million fatality-free shifts.’
Focused initiatives include introducing large-scale cover support as well as blast-on-mesh, rock nets and bolting, which have significantly reduced fall-of-ground injuries.
It’s not all down to driverless trucks and robotics, though. IoT enables the interconnectedness of various mining equipment and systems, facilitating predictive maintenance and early detection of equipment failures.
Software solutions and data digitalisation are being integrated into modern mining operations, serving as essential assets in strengthening safety measures, addressing risks and reinforcing safety protocols. Integrated safety management software allows mining companies to streamline safety procedures, monitor incidents in real-time and take pre-emptive actions.
Real-time monitoring systems, sensor technologies and wearable devices provide valuable insights into workers’ well-being, environmental conditions and potential hazards. Through software analysis, this data enables proactive decision-making, early identification of risks and the implementation of measures for a safer working environment.
The Mineware Syncromine software package, for instance, provides across-the-board functionality and reporting capabilities. Big data is captured through real-time monitoring from various sections within the mining operation and presented in detailed reports, providing essential insights.
Mobile apps are also contributing to the journey to zero harm, making strides in areas ranging from planning to the prevention of fatalities and injuries. The main advantage of using mobile devices offline lies in their mobility and ability to maintain connectivity, even in remote underground areas. This enables immediate logging of accidents or work orders on-site.
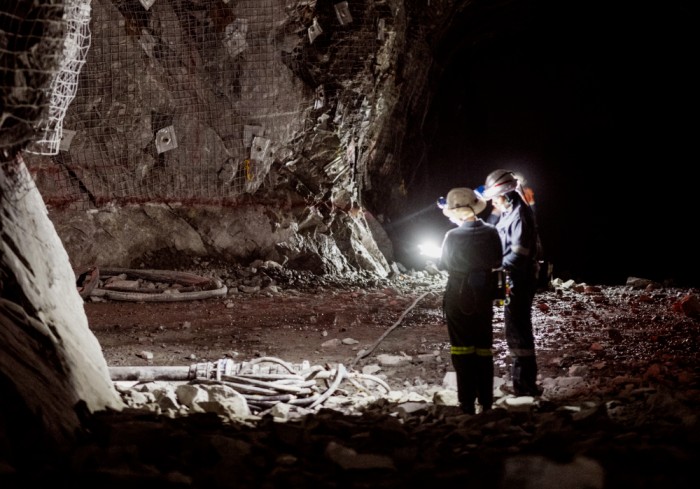
Syncromine software, for instance, includes a safety module that digitalises various mining processes, serving as a hub for collecting and managing critical information related to mine-safety management and asset tracking. It helps manage daily risks through real-time updates on outcomes from risk assessment checklists, prompting immediate action on any identified non-compliances.
In July 2023, the open-cast Phalandwa colliery in Mpumalanga became the continent’s first 5G-enabled mine, which has improved safety and efficiency by ensuring guaranteed connectivity within the mine and plant area.
The deployment of more applications has yielded proximity detection systems, vehicle detection, tracking and wireless video surveillance. At the time, Phalandwa GM Kgotso Mongalo said that ‘being a 5G-enabled mine helps us in real time when it comes to the detection of accidents from machine-to-machine and man-to-man’.
With the pursuit of zero harm always at the forefront, miners must continue to invest in cutting-edge technologies and engage with stakeholders to ensure a safer and more sustainable future for all involved.